ダイレクトギヤミーリングホブレス歯車製作
素材からダイレクトに歯車を削り出すダイレクトギヤミーリング
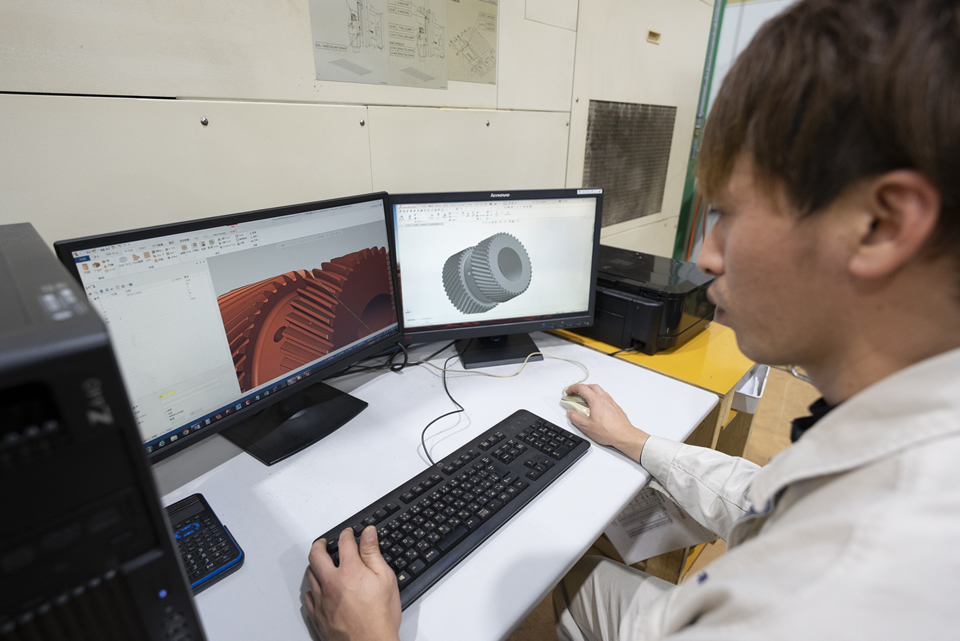
独自プログラムでホブ加工と
同一の「完全創成加工」を実現
ダイレクトギヤミーリングとは、ホブ加工を忠実にトレースする独自のNCプログラムを使いNC加工機でダイレクトに歯車を削り出す加工方法になります。
従来のホブを使って歯車を製作する加工方法を忠実にトレースして歯車を削り出すことでミクロン単位での超高精度歯車の製作が可能です。
さらに、NC機の自由度により、"ホブ" のトレースする位置から微妙に "外す"ことで歯車に必要な"クラウニング"などの歯面修正を行うことが可能です。
ダイレクトギヤミーリングはホブの原理を応用していますが、ホブの精度を遥かに超え、歯面研削に近づこうとする加工です。
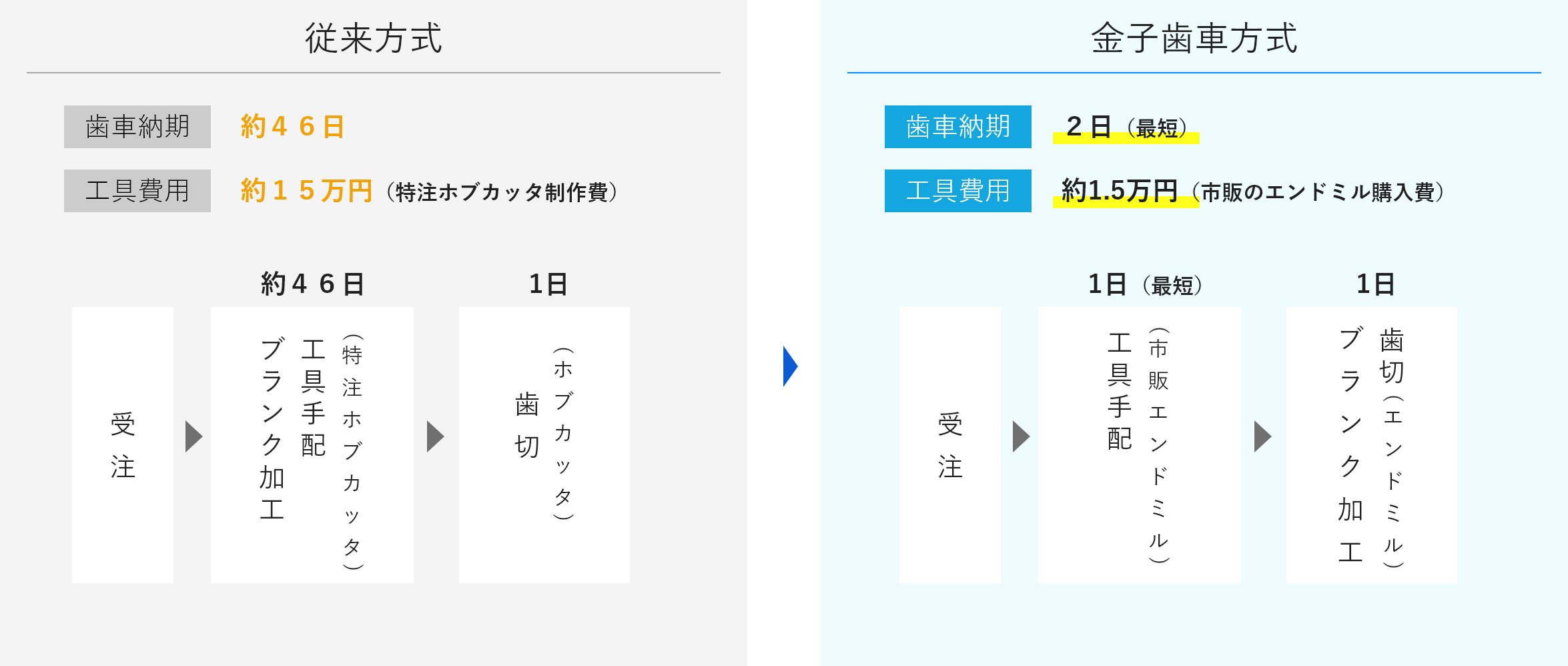
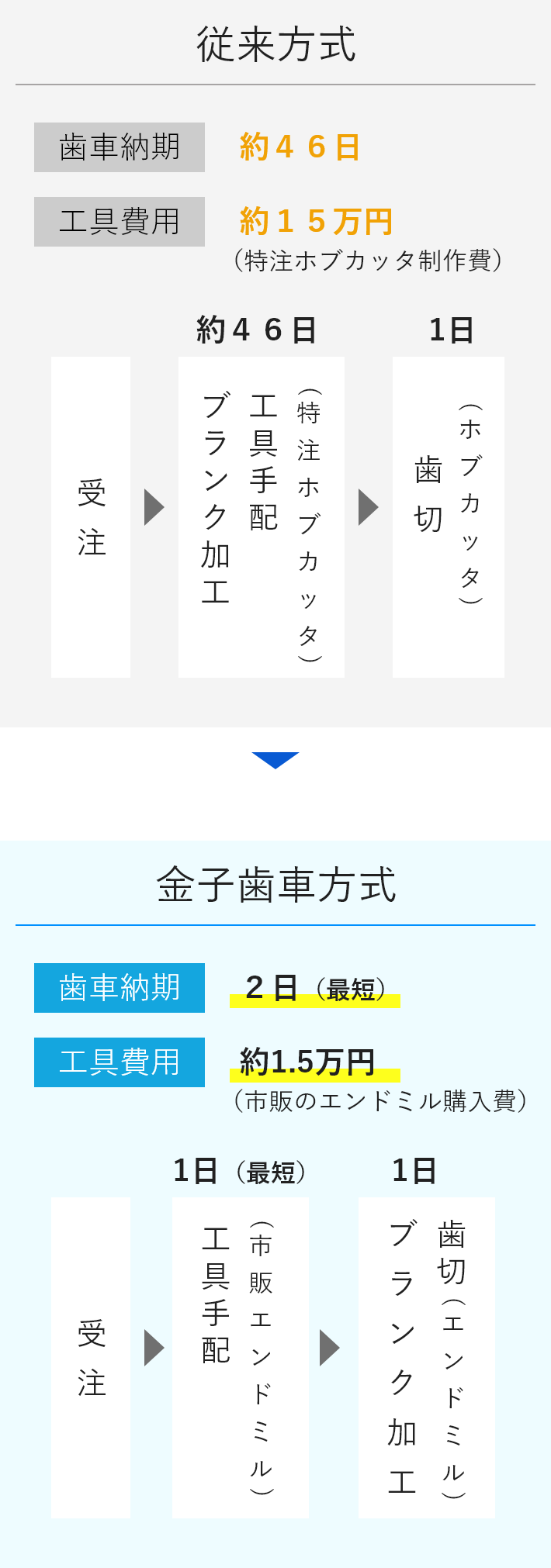
3DCAD/CAM+NC加工機による歯車加工とダイレクトギヤミーリングの違い
3DCADやCAMが発達し、NC加工機で見た目には普通の歯車を作製することは出来るようになりました。
しかし、静音静、低振動性を考えた場合、非常に精密な部品になり、自動車などで使用される歯車の歯面は数ミクロンのオーダーで仕上げなければなりません。
そのような状況ではボールエンドミルを使用する3DCADやCAMによる加工では限界があります。
当社のダイレクトギヤミーリングは、ホブがトレースする場所を忠実に再現するNCプログラムを独自開発し、ホブ加工と同一の創成路線を描き歯車を削り出します。
ホブ加工を忠実にトレースしたダイレクトギヤミーリングは、量産同等の高精度、高品質での歯車を短納期、低コストにて製作が可能です。
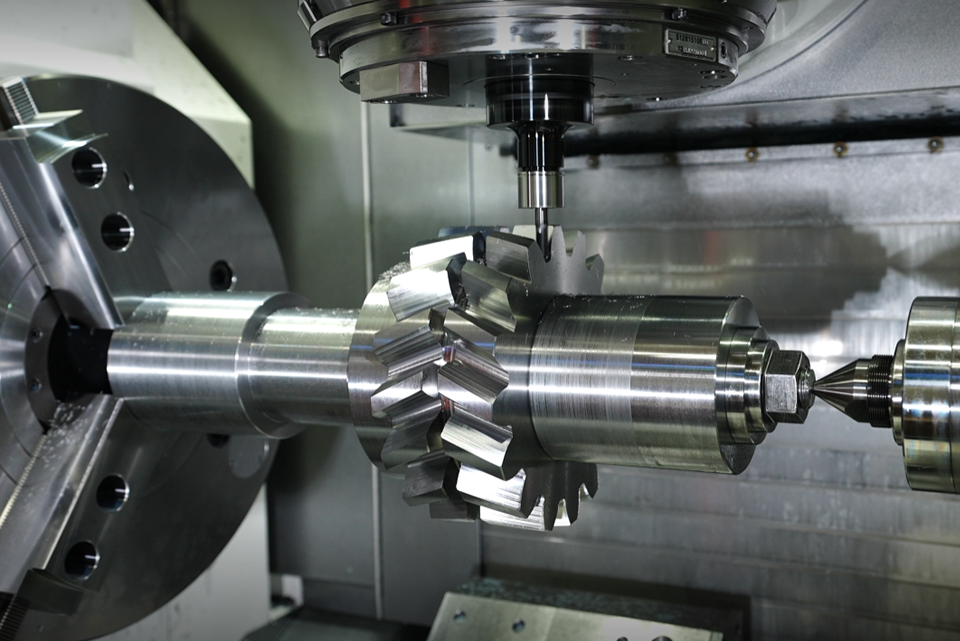
ダイレクトギヤミーリングの製作の流れ
加工データ作成・確認
-
STEP
01NCデータ作成
自社開発プログラムでNCデータ作成。
-
STEP
02創成図を作成・確認
ホブ加工による創成図を作成・確認。
-
STEP
03創成路線の確認
エンドミル加工による創成軌跡を作成し、ホブ加工にによる創成路線との一致を確認。
歯車の完成創成加工
-
STEP
04ワンストップ加工
複合旋盤一台で、ブランクから歯切りまでのワンストップ加工。
-
STEP
05歯切り加工
エンドミルによる創成歯切り加工。
-
STEP
06完成
素材からダイレクトに歯切りを行い完成。
ダイレクトギヤミーリングは、歯車技術研究所の木脇氏が、以前、弊社在籍中に開発した加工プログラムで、現在もタイアップして技術向上に努めています。
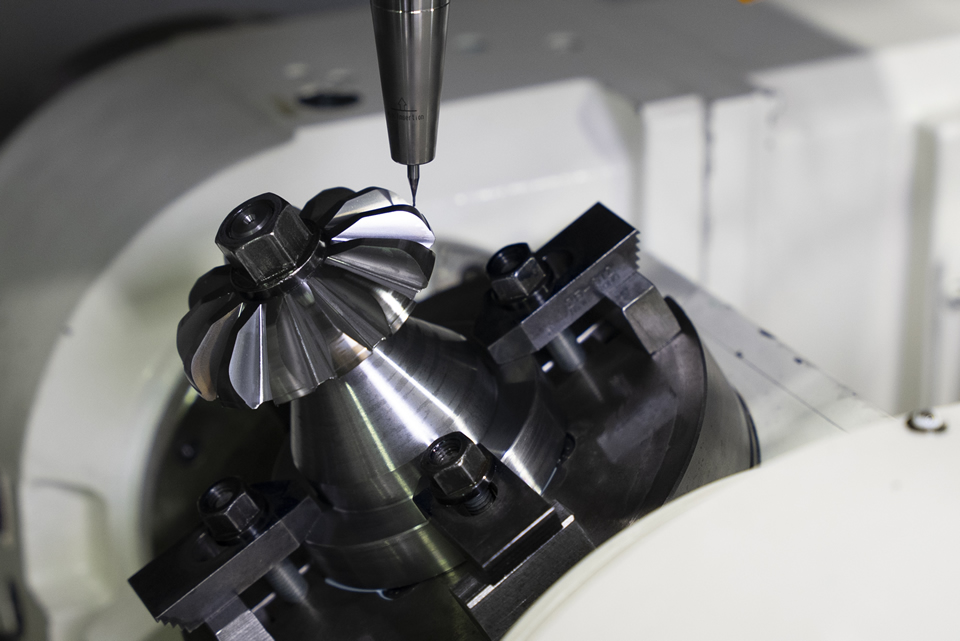
焼入れ後の高硬度歯面研磨加工
ダイレクト・ギヤ・ハードカッティング工法
歯車の高精度化の技術としてDGM工法を応用し焼入れ後の高硬度歯車の歯面研磨加工に変わるダイレクト・ギヤ・ハードカッティング工法を技術構築し、JIS0級レベルまで対応可能としました。高精度・短納期・低コストの新技術をご検討ください。
よくある質問
Q1個からでもお願いできますか?
もちろんです。ダイレクトギヤミーリングの特徴は特殊な歯車諸元の歯車を 短い工期で作り上げる加工方法です。加工コストは少し割高になりますが、製品の製作コストや工期に加え、専用工具や治具を製作するコストや工期を必要としないことで、全体的なコストダウン、短納期に対応出来る製造方法です。
Qステンレス、アルミ、樹脂など鉄以外の素材を含む対応素材を教えてください。
基本的に超硬エンドミルを使用し加工を行いますので、一般的な歯車加工用ホブ(ハイス)に比べ市販されている適正な工具を選定することが出来、様々な素材の加工に対応します。
Q熱処理、焼入れ、表面処理など一貫して対応していただけますか?
社内での工程ではありませんが、全国に点在する協力会社にて対応します。熱処理、焼入れ、表面処理のエキスパートに協力してもらい製品を仕上げていきます。
Qどんな種類の歯車に対応していただけますか?
平歯車(スパーギヤ)、はすば歯車(ヘリカルギヤ)、やまば歯車(ダブルヘリカルギヤ)、すぐ歯傘歯車(ストレートベベルギヤ)、まがり歯傘歯車(スパイラルベベルギヤ)、ハイポイドギヤ、ウォームギヤ・ホイール、ラックギヤ、スプロケット、プーリー、様々な歯車に対応します。全ての歯車の歯型に対応します。
Qおおよその納期を教えてください。
製品の製造過程によりますが、特殊歯車の特殊歯型を市販工具で対応しますので、工具の調達、プログラムの作成から加工までを最短3日から5日程度で対応します。その後、焼入れや研磨などの工程を加算して製品の完成を迎えます。